Cleaning E2 crates: Choosing a manual or an automated process?
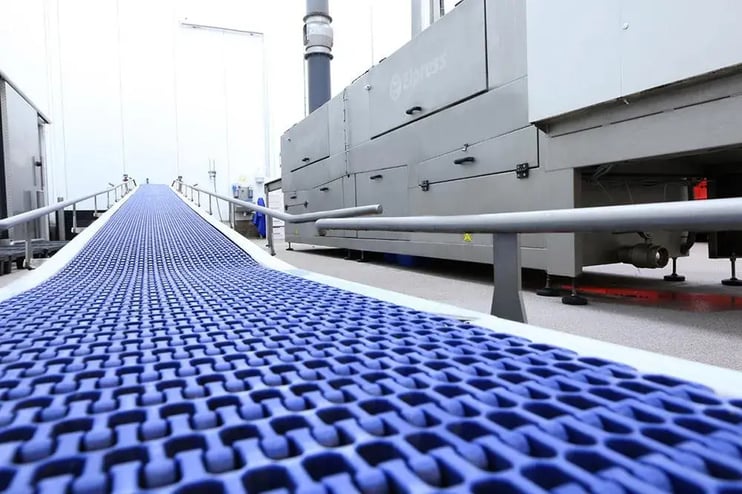
The logistics process around cleaning E2 crates can be designed in two different ways: manual input and output or with fully or partially automated handling. The number of crates to be cleaned is all-important when making this choice.
E2 crates are load carriers that are often used for the distribution of products in the meat processing and poultry processing industry. The standard format of this Euronorm crate is 600x400x200 millimeter. Within the E-series crates with other heights are also available: The E1 crate (125 millimetres high) and the E3 crate (300 millimetres high). Because of its large volume (60 litres) this last type is less practical and therefore also less popular.
E2 crates: simple to clean
E2 crates have four closed sides and have a very smooth finish. Therefore they are very hygienic in their use, simple to clean and dry quickly. The crates can be fed in widthways into a standard crate washer that has a track width of 600 millimetres.
Manual versus automatic
The choice of manual input and output or a partial or totally automated process is determined in particular by the number of crates that need to be washed. Up to approx. 500 load carriers per hour – that is 4.000 crates per day based on an 8-hour working day – a manual process is still feasible.
Do you want to wash more than 500 crates per hour? Then it would be wise to consider an automated process. You can determine whether this is profitable by comparing the investment costs for this process to the labour costs for a manual process. Do you have cheap labour? An automatic process will then be a less interesting investment.
Also, if there are less than 500 crates per hour to be washed, an automated process remains an option. Whether that is the choice depends mainly on the company's philosophy. The key question then is: 'What part does automation play within the management of the business?
Combined process: logistic and cleaning process at once
It is also possible to automate part of the logistics process. For example, at many companies the load carriers are brought in manually and only the process after washing is automated. Via a conveyor belt and with a stacker the clean crates are then automatically stacked onto a pallet. To also automate the process that takes place before the crates go into the washer, a de-stacker is needed that removes the crates from the pallet. Via a conveyor belt the crates are then transported to the washer. Depending on the route that the crates must follow, automatic tippers can also be added to the logistics process. Naturally the place where the crate washer is going to be placed within the company building must be carefully considered, so that the logistics process runs as efficiently as possible.
Crate washer calculator
Besides the decision concerning whether you would like a manual or an automatic logistics process, it is also important that you make the right choice when selecting the crate washer itself. Would you like to know, quickly and simply, which crate washer suits your company best? Then please fill in the crate washer calculator and you will receive made to measure advise.